Песчаный асфальтобетон состоит из битума, бетона, песка или щебня и минеральных составляющих. Все компоненты перечислены в ГОСТ 9128-2013, где также сформулированы различия по асфальтобетонам.
Типы смесей
По минеральным примесям разделяются на: песчаные, гравийные, щебеночные.
В качестве вяжущего вещества берут битум. И именно по его характеристикам определяют качество получаемого асфальтобетона.
Разделение по температуре: холодные – от 5 °С, горячие – от 110 °С;
Разделение по минералам, учитывая размер частиц:
- крупнозернистые – до 40 мм;
- мелкозернистые – до 20 мм;
- песчаные – до 10 мм.
Разделение на категории по количеству щебня:
- А – в ней его до 60%;
- Б – 50% щебневых соединений;
- В – до 40% соединения;
- Г и Д – щебня не содержится, в них входит песок;
- Г и Гх с песками из отсева;
- Д и Дх с природными песками, добытыми в карьере.
Также они бывают пористые, высокопористые, плотные, высокоплотные.
Асфальтобетоны могут быть таких марок:
- для горячих составов: категории Г – I, II, III; Д – II, III;
- для холодных составов: Гх – I, II; Дх – II.
Свойства
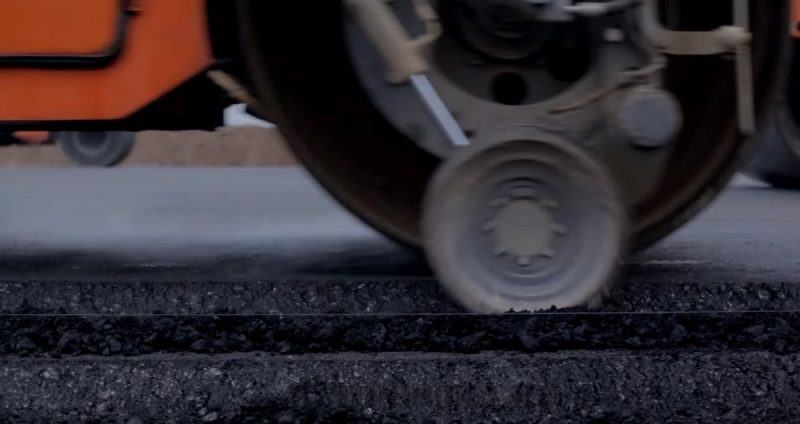
Укладка песчаного асфальтобетона
Составы должны обладать такими физико-механическими свойствами: предел прочности при сжатости для горячих составов, марки I будет равен 0,7 и для II – 0,5, сжатие проводят при Т=50 °С, сопротивление действию воды соответственно будет 0,7 и 0,6. Для холодных предел прочности при сжатости до нагревания сухих составов по марке I будет 1,5 по марке II – 1,2; после нагревания соответственно 1,8 и 1,5.
Содержание пустот, трещин в минеральных добавках холодных смесей будет 21%. Однородность асфальтобетона определяется коэффициентом водонасыщения для марок I, II будет равна 0,15. Она не может быть выше ±0,5% от всего веса.
Пески подбирают, учитывая ГОСТ 8736-93 и ГОСТ 3344-83, прочность и глинистые включения приведены в таблице.
Таблица 1 – Требования к свойствам песка
Показатель | Применяется в составе и используемые марки | ||
I | II | III | |
Для гор. и хол. типов | Для гор. и хол. типов | Для горячих типов | |
Г, Гх | Г, Д, Дх | Г, Д | |
Прочность песка, полученного из отсева гравия и горных пород, не менее | 1000 | 800 | 600 |
Присутствие глинистых частиц, % по массе (определяется методом набухания) | 0,5 | 0,5 | 1,0 |
Добавки минералов берут по ГОСТ Р 52129-2003, на нефтяные битумы распространяется ГОСТ 22245, на жидкие – ГОСТ 11955.
Состав и изготовление
Асфальтобетон состоит из: песка, порошков минерального происхождения, битума, полученного из нефти, и модифицирующих веществ. Также применяют горные породы, такие как: ракушечник, доломиты, известняки и другие; промышленные отходы: золошлаковые от ТЭС, от изготовления серы, асбеста и ряда других производств.
Минеральные вещества в составе асфальтобетона повышают качество. Количество минерального порошка должно быть точно рассчитано, т. к. если его добавить больше, чем положено, снизится прочность, особенно при низких температурах.
В результате применения добавок образуется единая структурная масса, меняются свойства: появляется способность выдерживать большие механические воздействия без деформаций, повышаются теплоустойчивость и прочность. Вышеперечисленные свойства увеличивают срок службы дорог, а это экономически выгодно. Для усиления применяют активированные и неактивированные составы.
Величина зерен минеральных добавок не менее 0,075 мм, их содержание в составе от 70 % до 80 %; крупных (от 0,3 мм) разрешается до 90 % от всей массы, а от 1,18 мм – до 100 %. Влажность – всего 1 %. Смешивать добавки разных фракций допускается, если температура вязкости битума 0,17 Па·сек (подогревать и смешивать минеральные составляющие, руководствуясь ГОСТ 12801-98).
Изготовить смесь можно только на специализированных заводах. Такой завод состоит из следующих узлов:
— узел хранения минеральных добавок;
— узел плавления битума;
— узел производства продукта.
При выборе необходимой марки, нужно изучить ее составляющие, стоимость и затем под условия эксплуатации дороги подобрать нужную. Чтобы покрытие служило дольше, заводы-изготовители в составы вводят добавки, повышающие пластичность, вязкость, уменьшающие хрупкость.
Чтобы изготовить состав необходимо соблюдать технологический цикл:
- Разогрев битума до 80-100°С в котлах первичного нагрева, затем в битумно-плавильной установке доводят его температуру до 120 °С и, постоянно мешая, выпаривают влагу.
- Степень подготовленности битума определяет лаборатория.
- Подача битума в котлы и доведение до 16 °С, затем перекачка на весовую дозировку.
- Сушка минеральных добавок и смешивание с битумом.
- Подача дозированных минеральных веществ в элеватор.
- Сначала сухие минеральные составы просто перемешивают, потом нагревают и смешивают с битумом. Время смешивания для песка составляет около 180 сек.
- Выгрузка готовой смеси.
Область применения
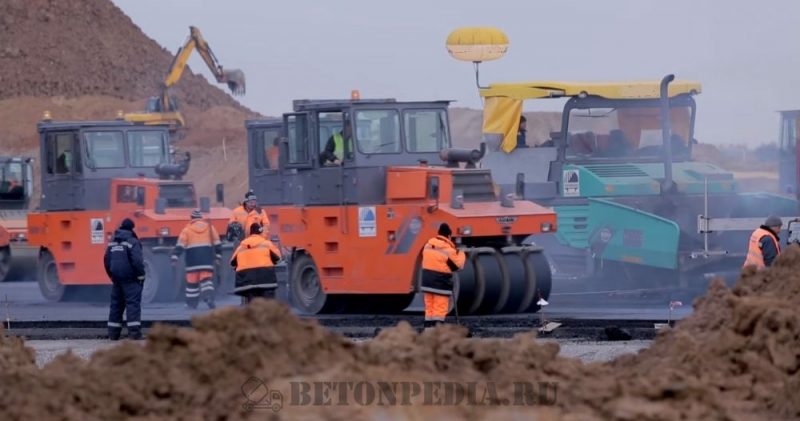
Применение песчаного асфальтобетона для укладки дорог
Применяются асфальтобетонные смеси для покрытий дорог. Выбор для этих целей асфальтобетона объясняется свойствами материала:
- Прочность к выдерживанию нагрузок.
- Сцепление покрытия дороги с шинами автомобилей.
- Отработанные технологии укладки этих смесей и достаточное количество предприятий, производящих их.
- Технология укладки позволяет получить ровную поверхность полотна.
- Снятые слои при ремонте можно переработать и снова уложить.
- Асфальтобетонные дороги более гигиеничны, чем грунтовые.
- Движение автомобилей по ним происходит без особого шума.
- Они легко поливаются летом, их удобно очистить зимой от снега.
- Ремонт покрытий будет дешевле и проще (в сравнении с грунтовыми).
Песчаный асфальтобетон кладут последним слоем на полотно дороги, тротуары, полы при возведении цехов, пешеходных дорожек. Толщину слоя, который нужно уложить, регламентирует СНиП 2.05.02-85. Для достижения долгого срока эксплуатации нужен определенный состав, учитывающий погодные колебания и нагрузку дороги.
Источники информации:
- ГОСТ 9128-2013 [URL: http://docs.cntd.ru/document/1200108509]
- ОДМ 218.2.034-2013 [URL: https://ohranatruda.ru/ot_biblio/norma/395780/]
- Технологическая карта для Д-325 (Д-125) [URL: http://www.gosthelp.ru/text/TexnologicheskayakartaTex7.html]
- Белый цемент - 16.11.2021
- Мытый бетон - 16.11.2021
- Фотокаталитический бетон - 16.11.2021